The Dualsun FLASH Shingle Black and SPRING Shingle Black solar panels are equipped with “Shingle” cells.
This next-generation cell technology brings multiple benefits to SPRING and FLASH panels.
- Better overall module performance:
- Optimized active surface
- Less hot spots
- Better efficiency in case of shading
- More resistant:
- Less internal mechanical stress on the module.
- Reliability certified by the TÜV control office and low impact of extreme conditions on photovoltaic performance.
- Better absorption of the pressure on the panel compared to traditional monocrystalline photovoltaic cells.
- Lower risk micro-cracks, thus lower decrease in yield over time.
- Exceptional design thanks to its “Ultra full black” look
- Lower environmental impact : less harmful metals* and improved recycling rate
*See explanations below
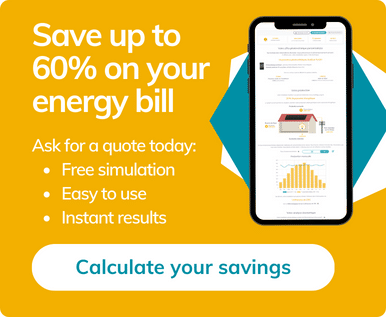
Available cell technologies on the market
There are currently several types of monocrystalline photovoltaic cell technologies on the market:
Shingle | Half-cut | Full size cell |
---|---|---|
![]() | ![]() | ![]() |
The most powerful Shingle cells which compose our SPRING Shingle Black and FLASH Shingle Black panels. | The “half cut”cells which are present on our FLASH Half-Cut White and FLASH half-Cut Black panels. | The “full cell”monocrystalline cells. |
Shingle cells are 5-piece divisions of G1 type full cells.
Improved surface yield thanks to the module density of cells
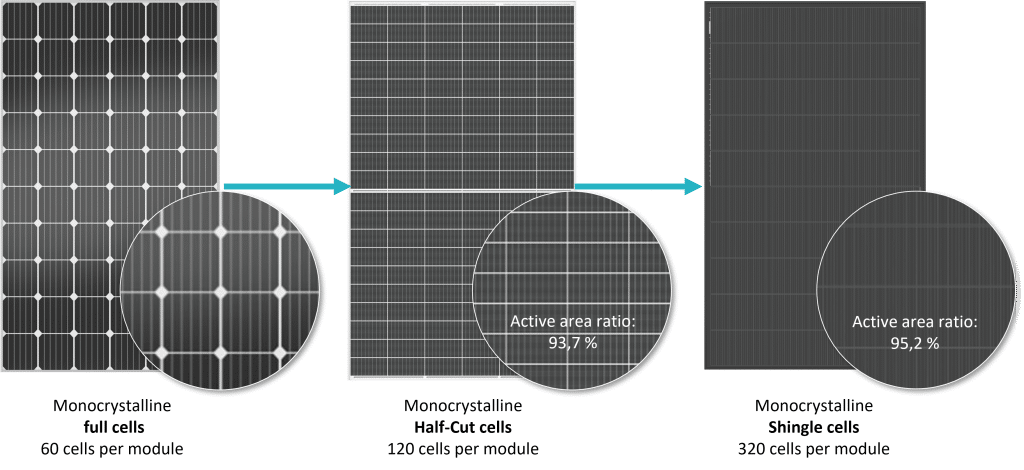
Better overall module performance thanks to low string intensity
Thanks toto their design, the cells of the FLASH and SPRING Shingle panels have an intensity 5 to 7 times lower than conventional monocrystalline cells.
Shingle cells are indeed divisions in 7 pieces of a type M12 full cell for the FLASH 425 Shingle Black, and 5 pieces of a type G1 full cell for the FLASH 375 Shingle Black.
This feature gives these panels a better performance than a conventional panel.
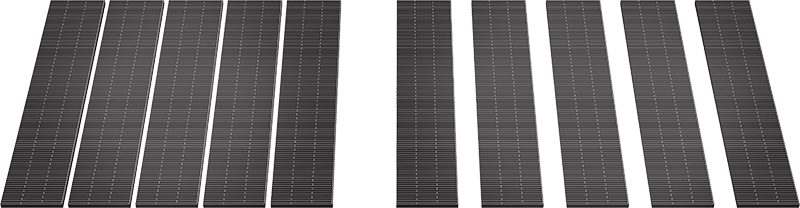
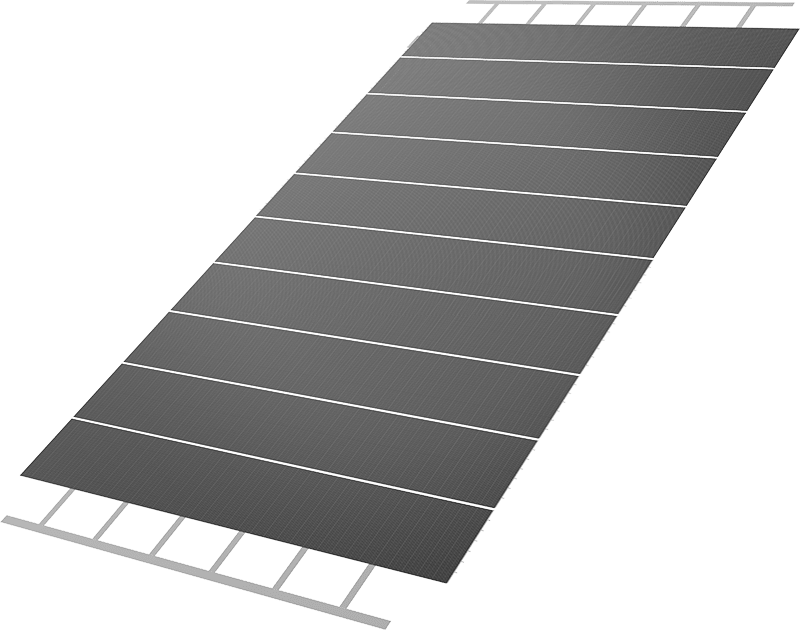
P= R x I²: The Joule effect losses are therefore significantly lower thanks to the Shingle technology.
This leads to an average operating temperature of about -5°C on the Shingle modules. Performance is improved.
Manufacturing of photovoltaic modules
Half-cut photovoltaic cells manufacturing process:
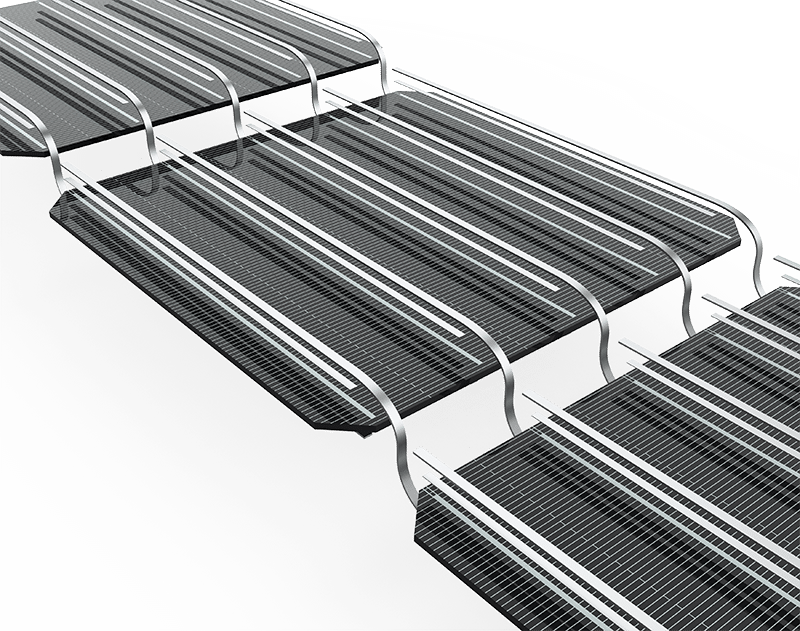
- Laser cutting of the full cells
- Strings laying out
- Interlocking
- Laminating
- Assembling
- Testing
Shingle photovoltaic cells manufacturing process:
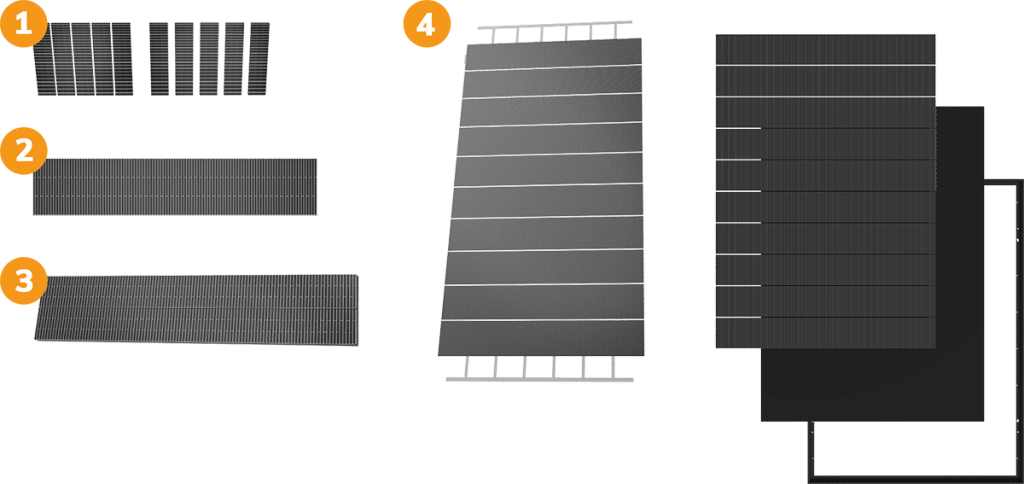
- Laser cutting of the full cells
- Setting up the Electric Conductor Adhesive (ECA)
- Positioning cells as tiles
- String laying out
- Assembling of the strings
- Laminating
- Testing
> Read more about the positioning of the by-pass diodes in the Dualsun Shingle panel.
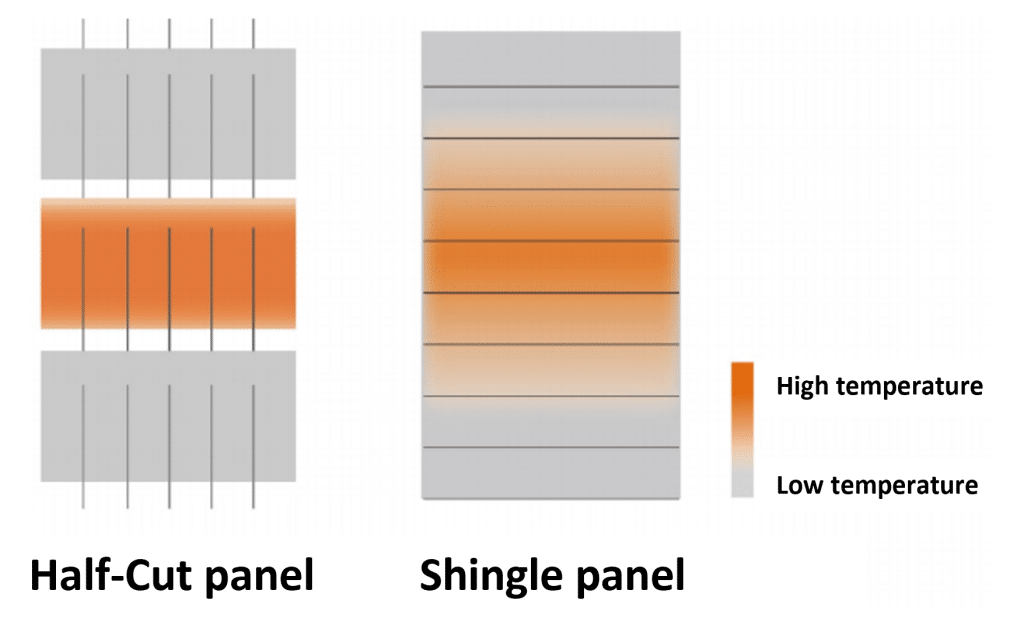
Thanks to this unique assembly of segmented cells and a fully parallel circuit, the module conducts heat with greater efficiency and with lower risk of hot spots.
The hotter the cells get , the less they produce (reduced voltage and current values). Furthermore, if the hot cell sets the operating current of the whole cell string (as is the case for full-cell and half-cut panels, but not for shingle panels), it impacts the efficiency of the whole string.
Better efficiency in case of shading
The cells of the Dualsun Shingle 375, 400 and 425 panels are organized in 10 parallel strings and in 2 groups.
This arrangement significantly reduces the negative effect of cell shading.
Indeed, in a shunt circuit, the main shunt current equals the sum of all the shunts’ current (law of additivity).
Concretely, if one of the 10 strings is impacted by shading, leaves or bird droppings, the intensity produced by the module equals the sum of the intensities of each string.
In other words, only the shaded string will see its production reduced, without impacting the production of the 9 other strings.
Note: As a comparison, on a full-cell or half-cut technology module, the module is respectively composed of 3 and 6 distinct parallel columns. The impact of shading is therefore more important on these technologies.

This graph helps visualizing the different impacts of shading on Shingle or Half-Cut modules:
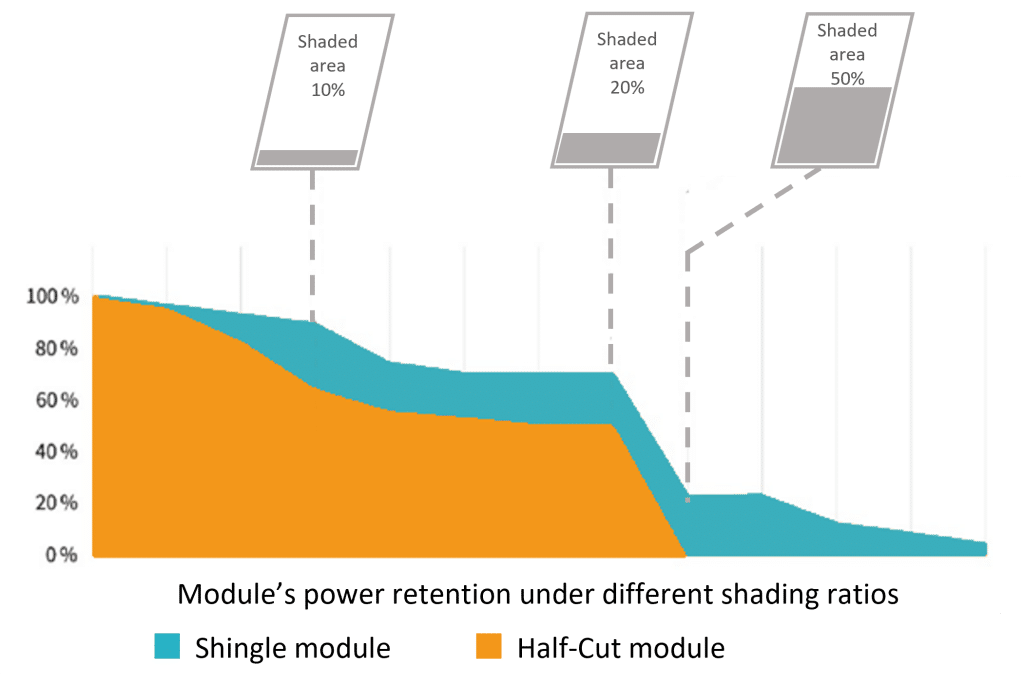
More resistant solar panels thanks to a decreased mechanical stress on the module
The FLASH and SPRING panels with Shingle technology incorporate an innovative cell interconnection process.
The low temperature and flexibility of the interconnection process removes the internal mechanical stress usually present in modules with high-temperature interconnections.
Standard photovoltaic technology
On standard panels, interconnections are done at high temperatures (250-300°C).
There are three possibilities:
- Either a great distance between the cells to relieve internal stress, however this reduces the surface yield.
- Or a reduced distance between the cells, but this induces a concentration of stress, which can lead to cracks of the cells.
- The third possibility is to have a negative distance between cells, which makes the cell crack risk even greater.
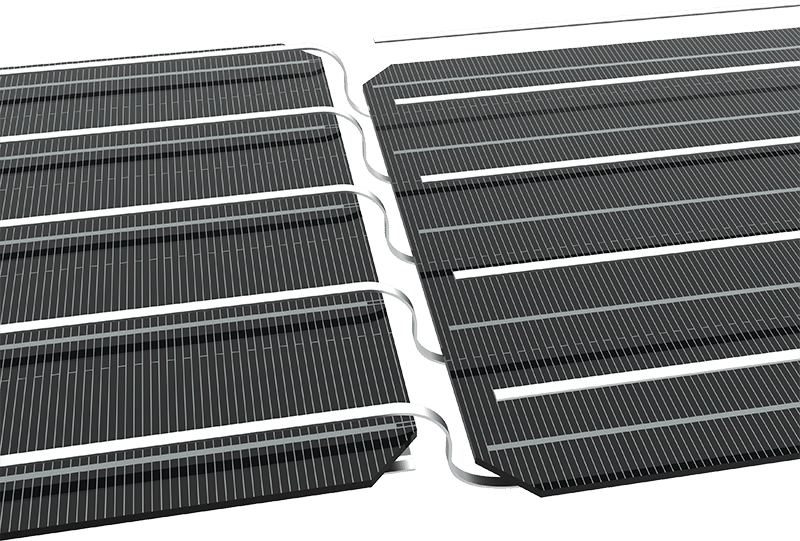
Shingle Technology
The Electric Conductor Adhesive (ECA) polymerizes at the same temperature as the module encapsulates: only 180°C. The thermal stress of the cells is therefore reduced compared to standard technologies.
The cells are interconnected with a flexible adhesive that incorporates an elastic energy absorption effect.
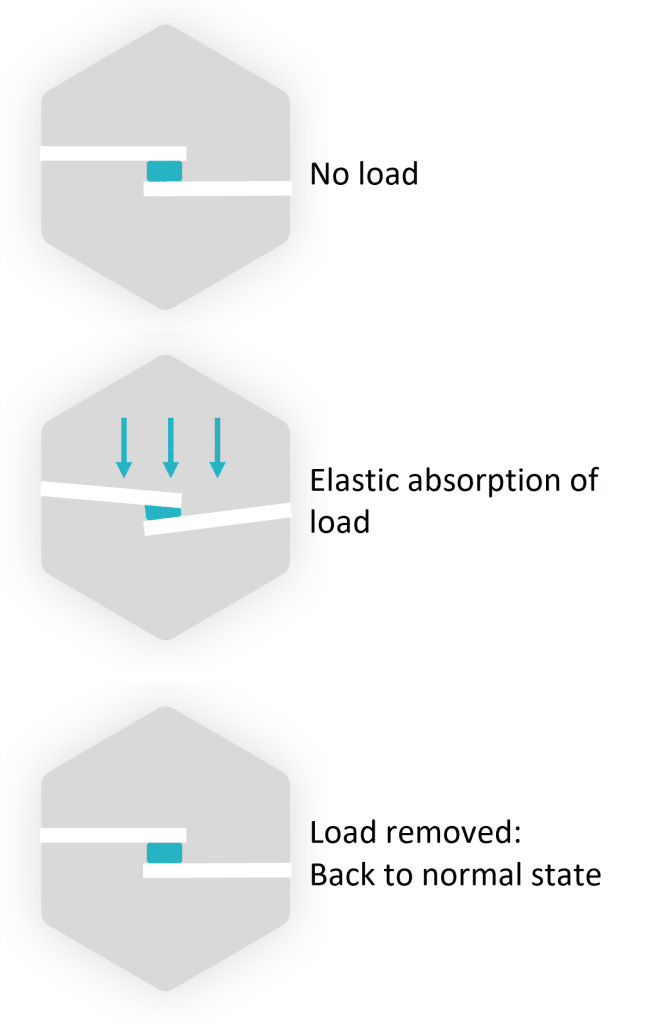
The Shingle module quality is certified by the TÜV and qualifies 3 times over what IEC standards require
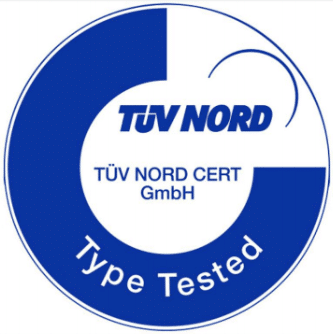
The very low impact when tested in extreme conditions is certified by the TÜV.
Even after performing 3 times the tests required by IEC standards, Shingle technology shows less than 5% loss of performance.
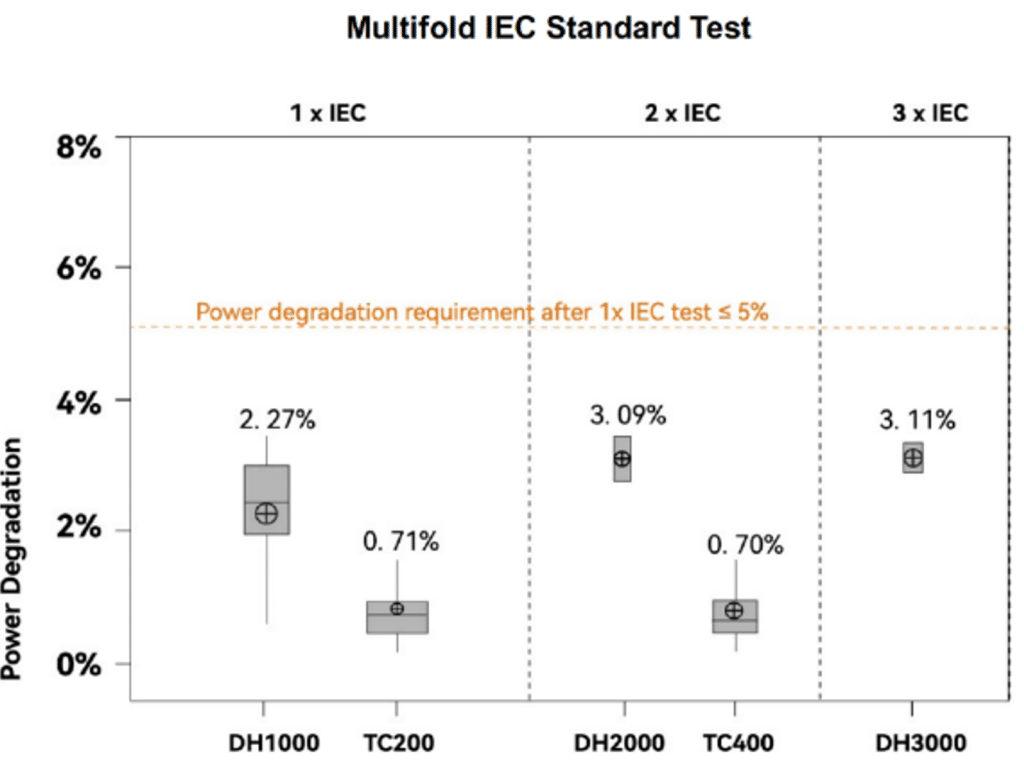
Shingle cells are less affected by micro-cracks
For various reasons, solar cells can undergo micro-cracks.
On a standard full cellorhalf-cut cell module with a micro-crack, a portion of the cell becomes isolated so the current no longer circulates through this area. This affects the efficiency and yield of the panel.
In the case of a FLASH or SPRING panel with Shingle cells, the continuity of the inter-connection allows the flow of electrons not to be affected, thus the yield of the module is maintained even in case of micro-cracks.
Shingle technology does not suffer pressure, it absorbs it
The behavior of cells under pressure
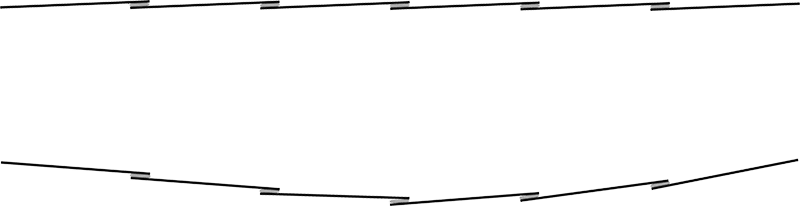
Shingle Technology
Under pressure, the flexible ECA of Shingle technology helps relieve the bending mechanical stress, keeping the interconnections intact.
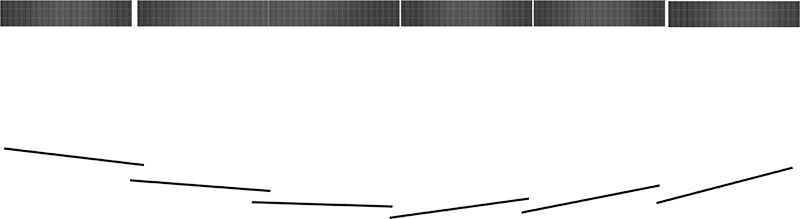
Standard photovoltaic technology
Standard photovoltaic technologies concentrate bending stress on the under pressure interconnection points, so the module performance decreases.
Low-temperature static mechanical load
Shingle technology is thus proved to be more resistant to low-temperature mechanical loads than conventional full cell or half-cut modules.
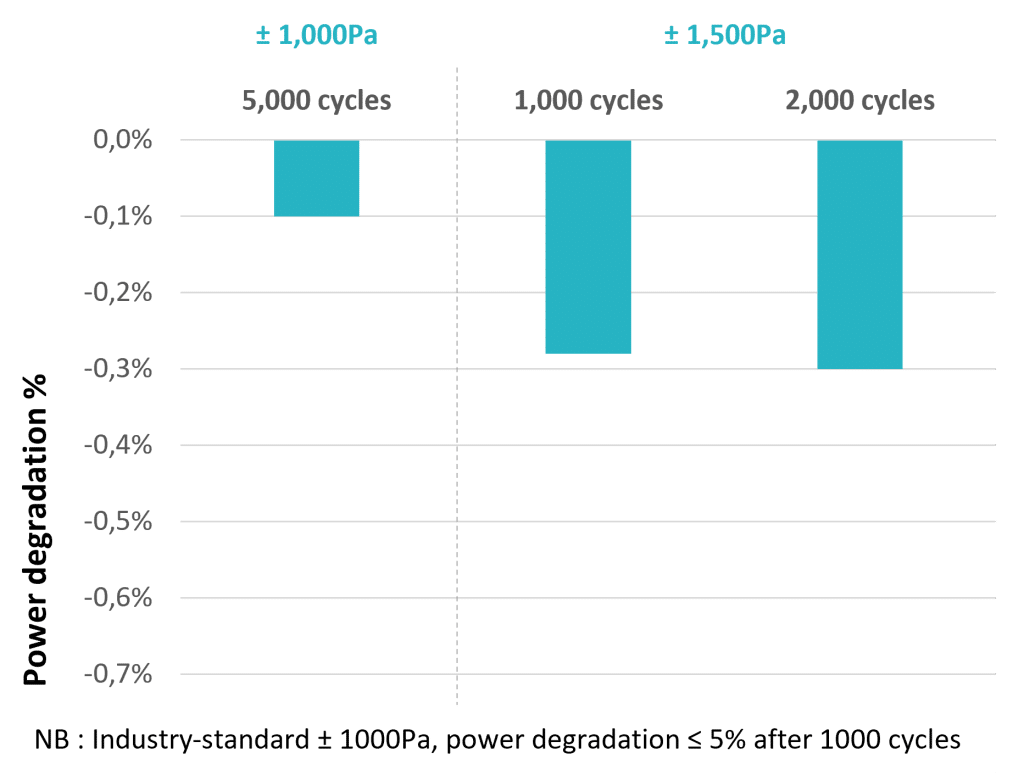
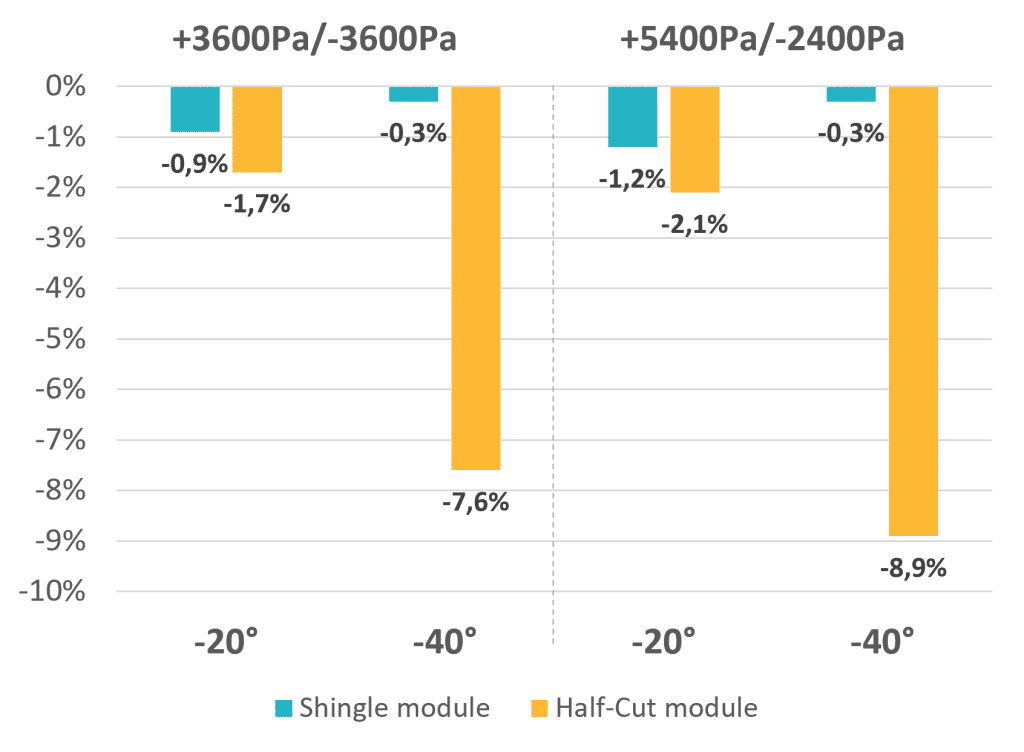
Lower environmental impact: less harmful metals and improved recycling rate
The absence of ribbon gridding all the cells on the front side of DualSun Shingle panels significantly reduces the presence of harmful metals, including lead, and reduces the thickness of the wafer and the amount of EVA.
The recycling rate of Shingle panels is thus improved.
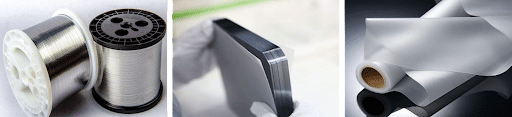
Lead consumption: -60%
Wafers thickness: -11%
EVA quantity: -31%

Exceptional design quality thanks to its “Ultra full black” look
The density of the module cells and the absence of ribbons on the cells provide a very uniform appearance to the Shingle panels which significantly improves the incorporation of the PV system on roofs.
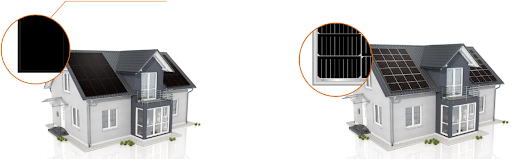
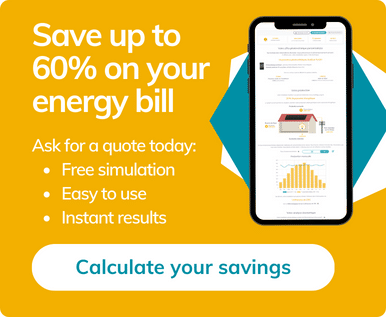
Aucun commentaire.
Leave a comment
Votre adresse e-mail ne sera pas publiée. Les champs obligatoires sont indiqués avec *